By Lindsey Putzier
Anyone who knows me even a little bit will tell you: blue is my favorite color. When I found out we would be dyeing items blue during my Provence trip, I was kind of ambivalent at first. Now after having finished, I can’t even express how fascinating and fun the dyeing process is!
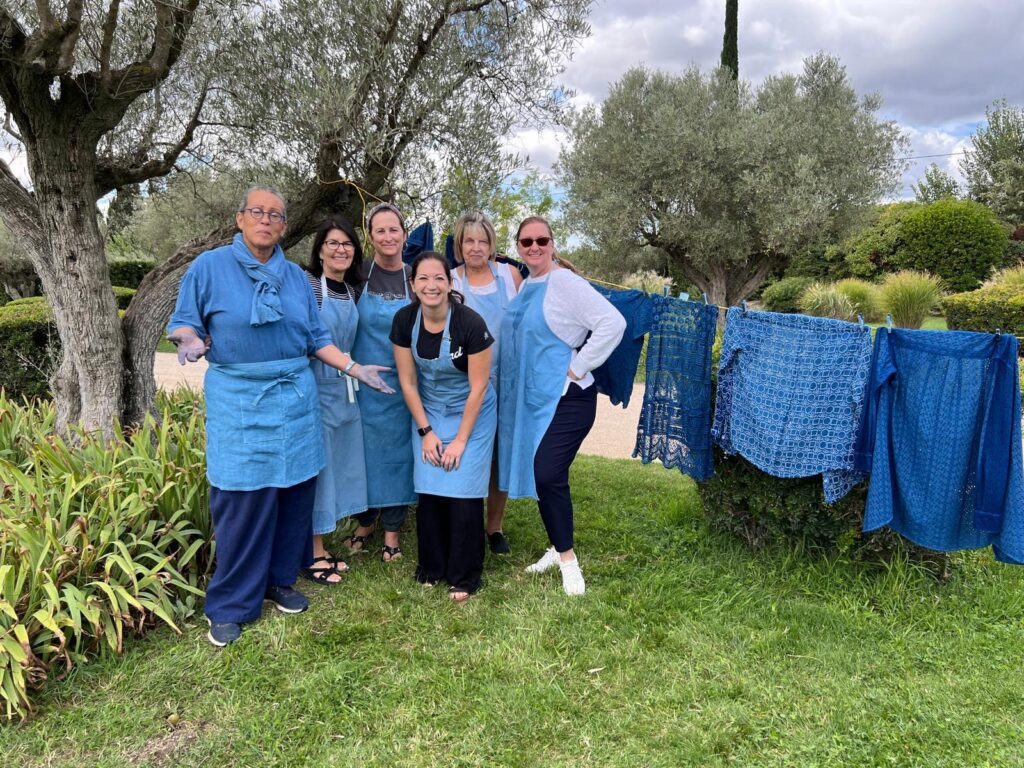
We were fortunate to have the world’s leading woad artisan, Denise Lambert, give us a personal tutorial on how to dye fabrics with woad. Denise and her late husband personally took on the challenge of reviving this lost art, spending years perfecting the process.
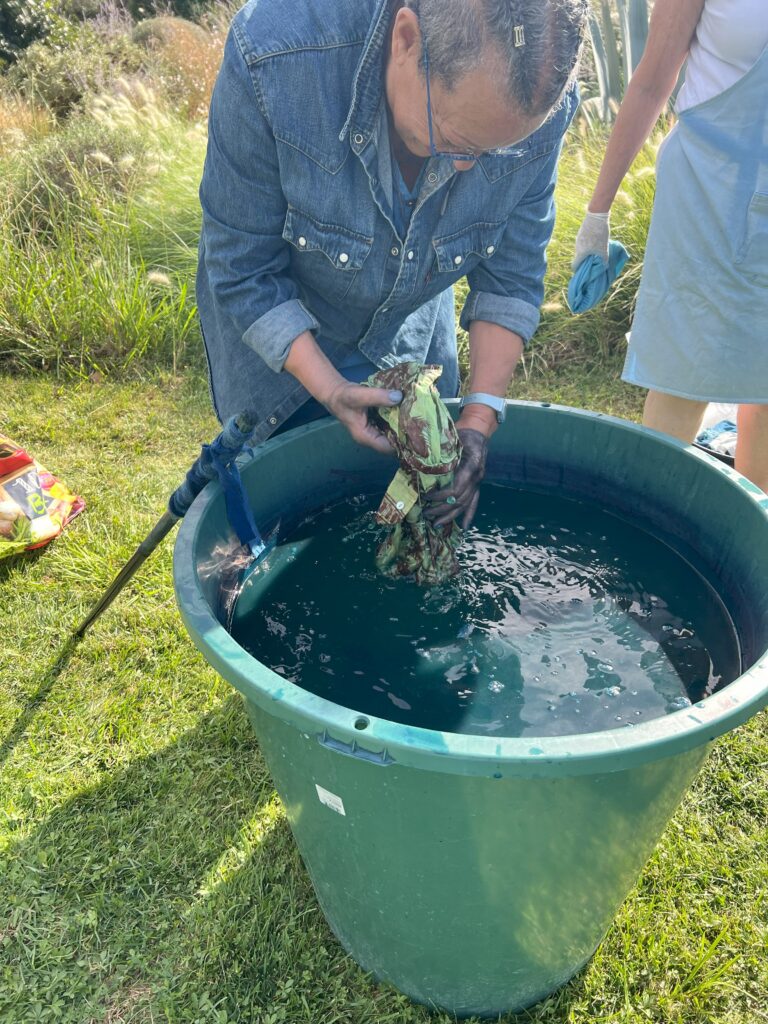
What’s woad’s history?
Woad’s cultural significance goes beyond just its use as a dye. In the past, it was a symbol of wealth and status, particularly in medieval Europe, where the production and trade of woad were important economic activities.
Woad dyeing is an ancient art that has been practiced for thousands of years by many ancient civilizations, including the Celts and Romans. The Celts famously used woad to paint their bodies for battle, while the Romans used it to dye textiles.
In the Middle Ages, woad became a valuable crop and a significant source of blue dye in Europe. Major woad-producing regions included parts of France, Germany, and Britain. Here’s what the plant looks like:
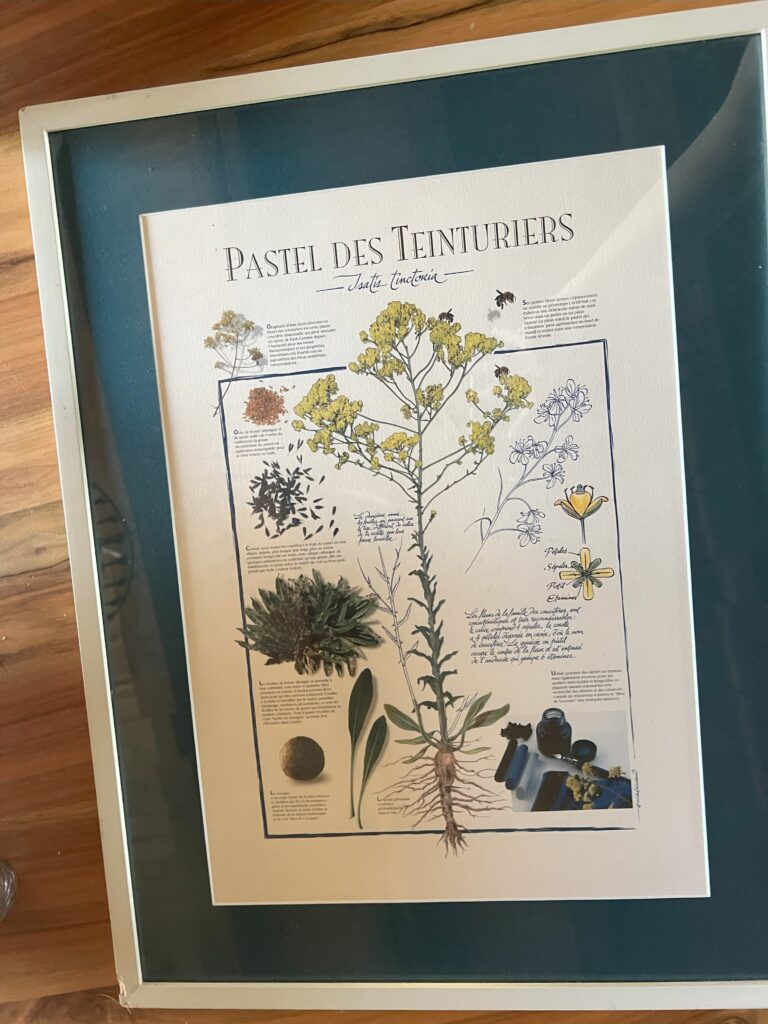
Woad was largely replaced by indigo in the 17th century, as indigo was more potent and produced a deeper blue. (Indigo on the left below. Woad on the right.)
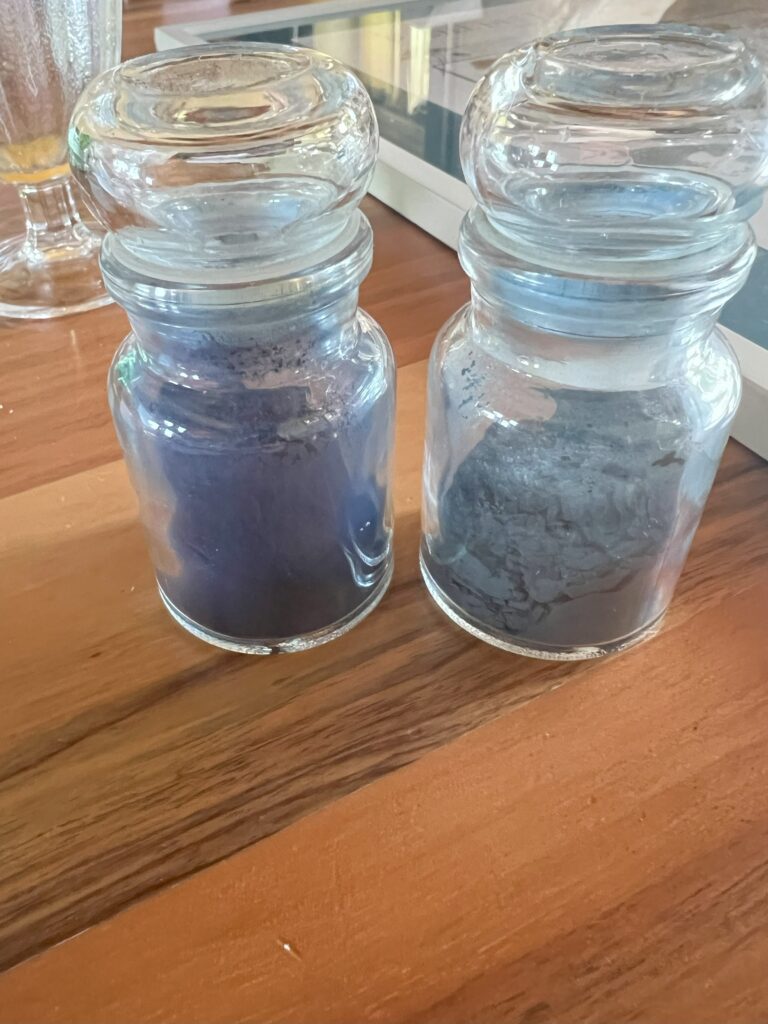
Indigo dye can also be kept in large vats and used for months, whereas woad only lasts a few hours.
Why use woad now?
Modern crafters use woad for dyeing fabrics, yarns, and even for artistic purposes, maintaining the ancient traditions while exploring new possibilities. Woad dyeing offers a glimpse into ancient craftsmanship, and its revival speaks to a broader interest in natural, sustainable, and historically-rooted textiles.
Here’s an example of an historic fabric, before and after woad dyeing.
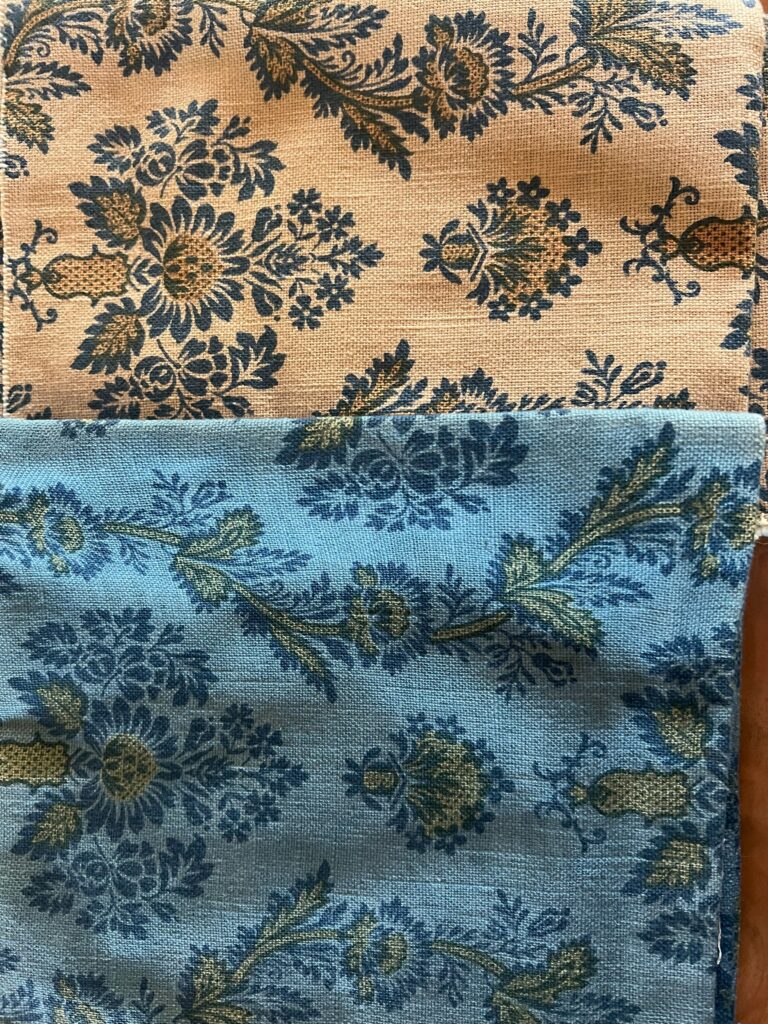
In recent years, there has been a resurgence of interest in woad dyeing, particularly in sustainable and natural dyeing practices. Small-scale artisans and textile artists appreciate woad for its eco-friendly and historical significance. I appreciate that it’s incredibly safe for hands and has medicinal qualities!
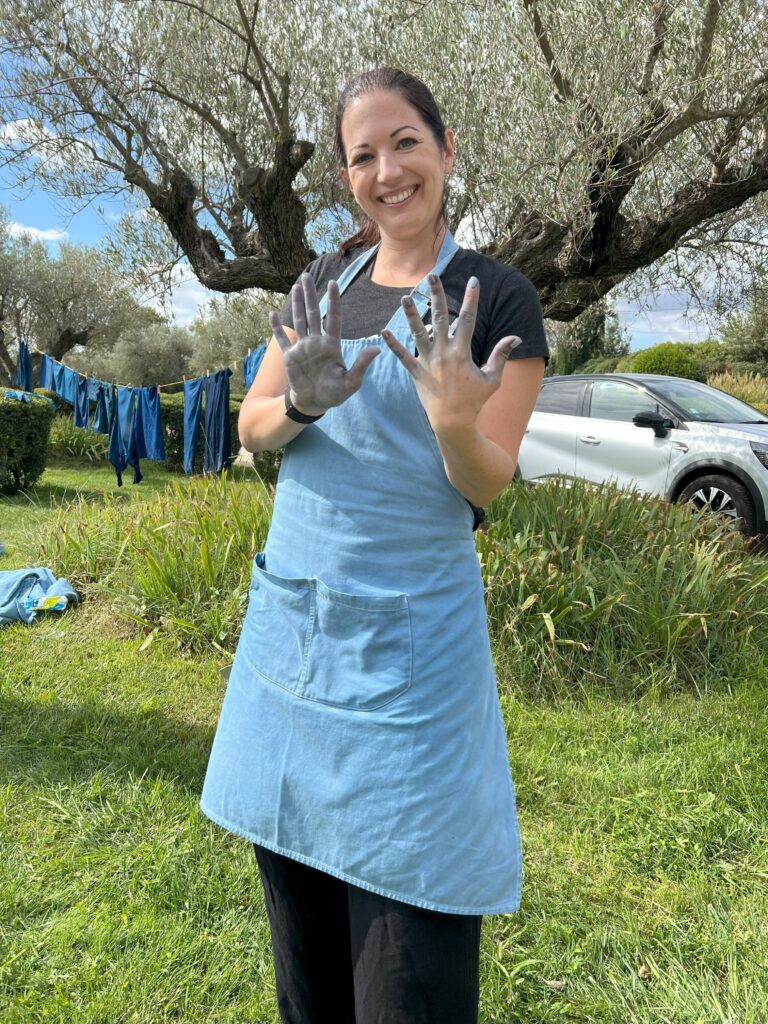
Woad-dyed textiles also have excellent color fastness, meaning the color holds up well to washing and exposure to light. Back in the day, sheets were literally boiled to be cleaned. Woad can be boilded hundreds of times without affecting the color. That’s not something you can say about cheap modern dyes!
How is woad made?
Woad (Isatis tinctoria) is a plant native to Europe, known for producing a blue dye. Woad dye comes from the leaves of the woad plant. Once harvested, the leaves are chopped, dried, and then processed.
On the left is a traditional woad “ball.” On the right, the ball has been broken up to prepare for dyeing.
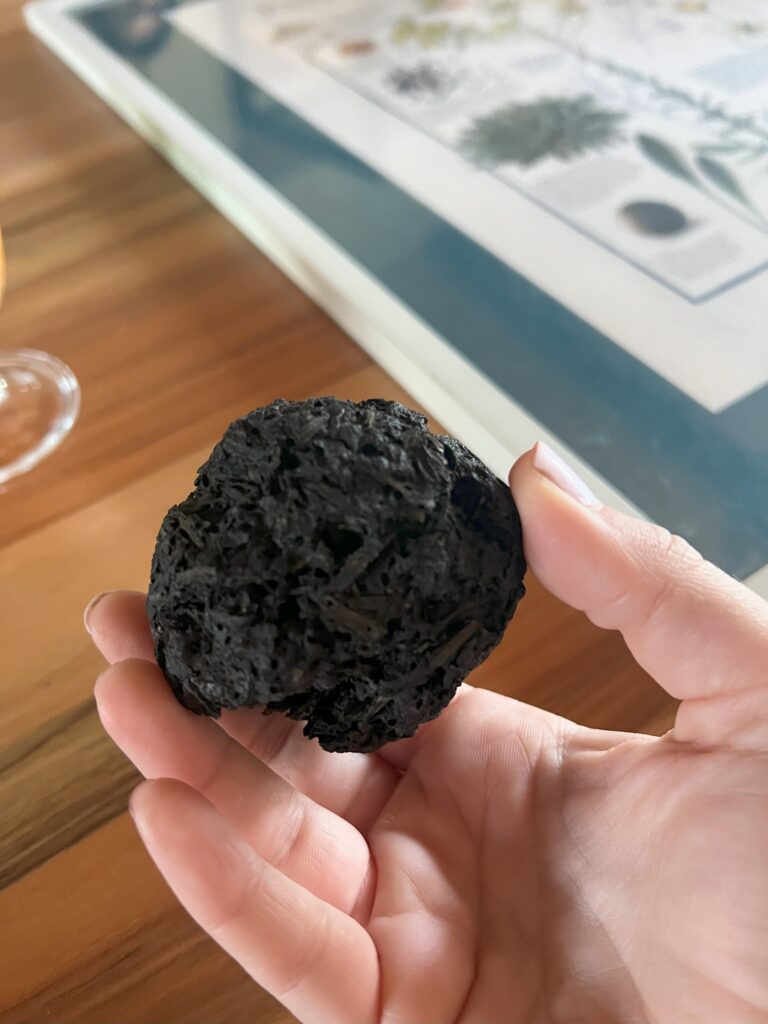
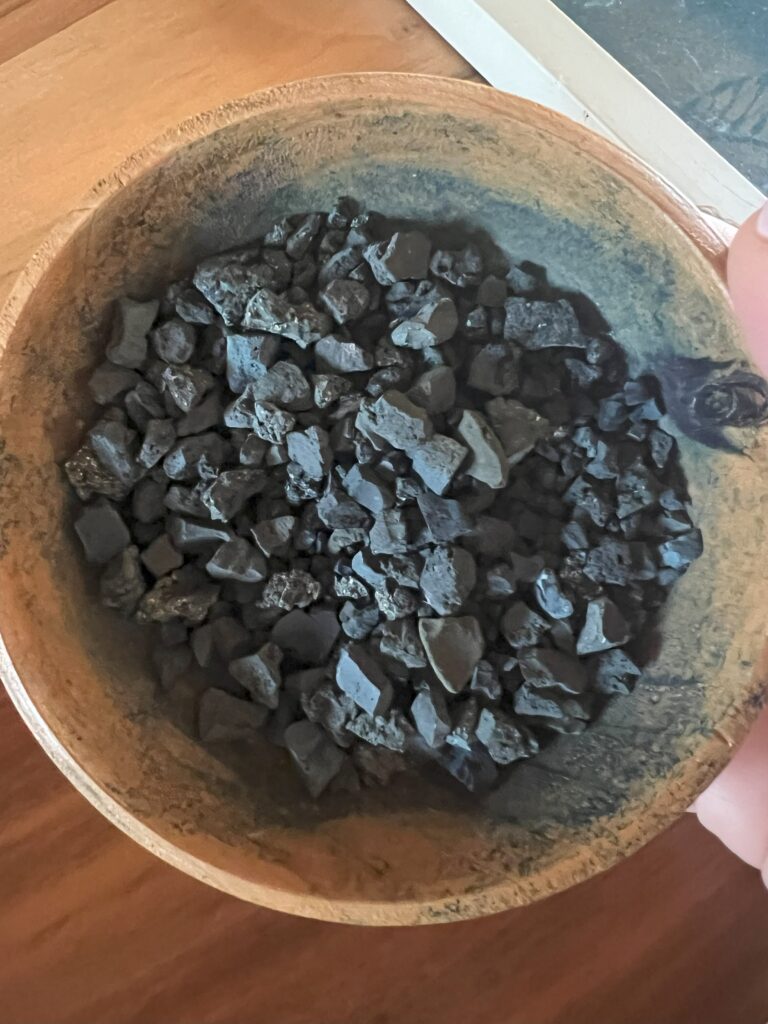
The dried leaves are fermented to extract the pigment. This fermentation process involves soaking the leaves in water, allowing bacteria to break down certain compounds and release the indigo precursor.
The extracted pigment is processed into a dye vat, which undergoes a reduction process (a chemical transformation where oxygen is removed). In this reduced form, the woad dye appears yellowish-green, rather than blue.
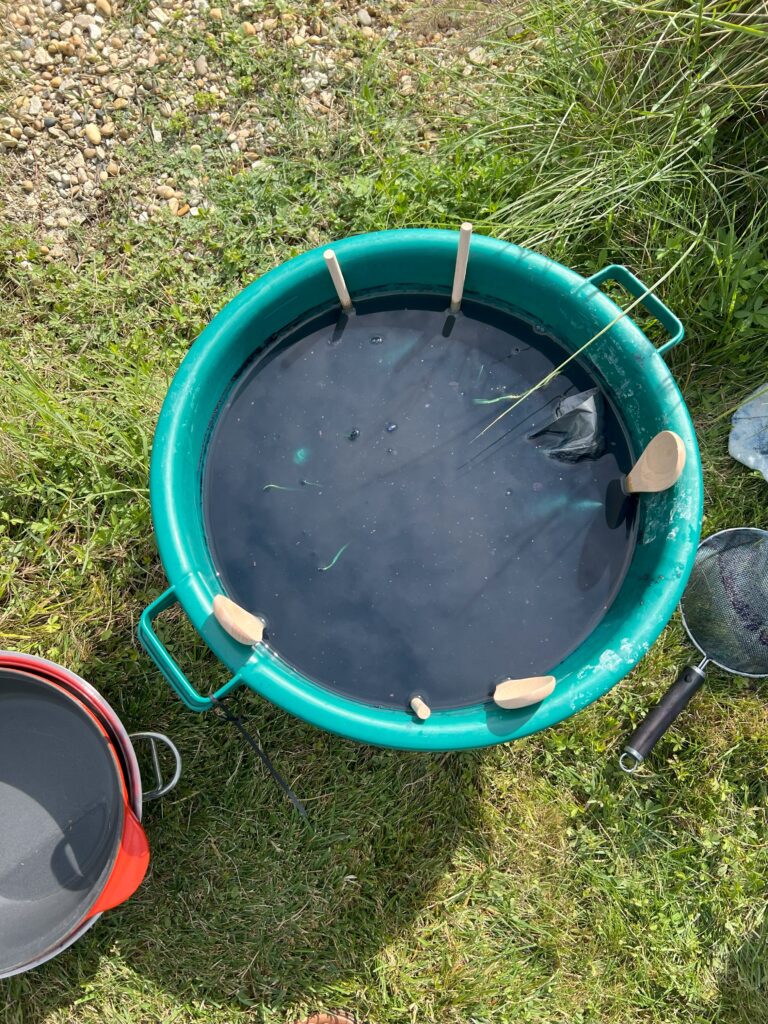
The color is honestly hideous when you first take the fabric out of the dye vat. However, you can watch the fabric change from nuclear yellow to deep green to blue in a matter of seconds sometimes!
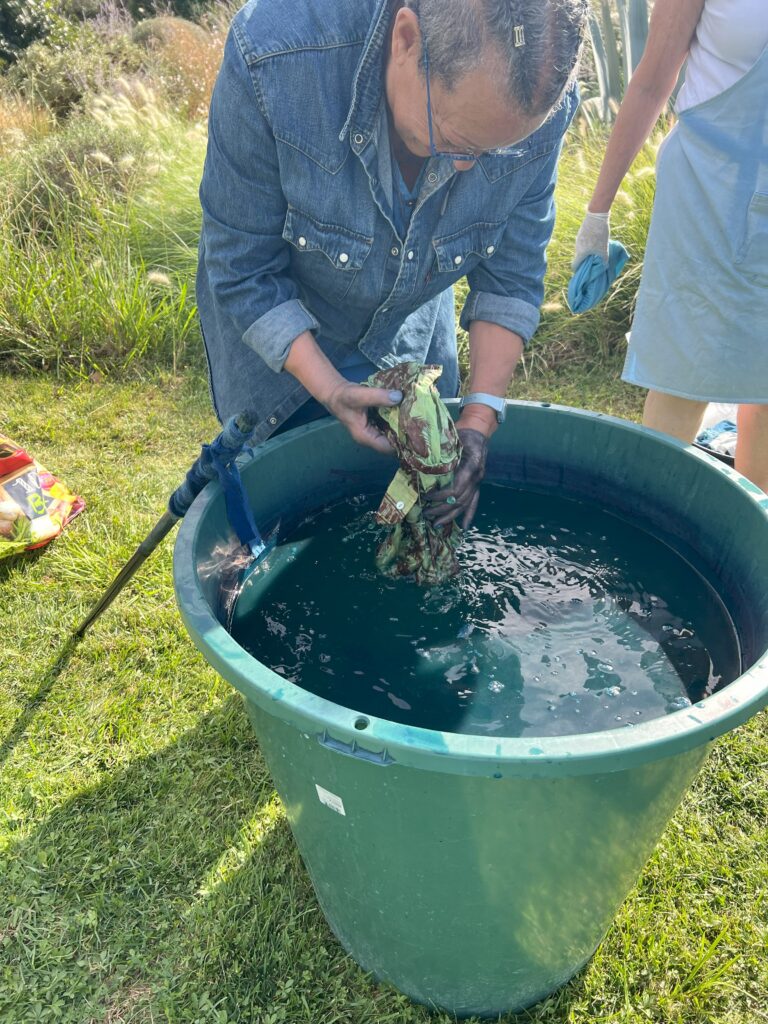
For darker or more intense blues, the fabric may be dipped several times. We dipped each item at least three times. Here’s a before and after for comparison:
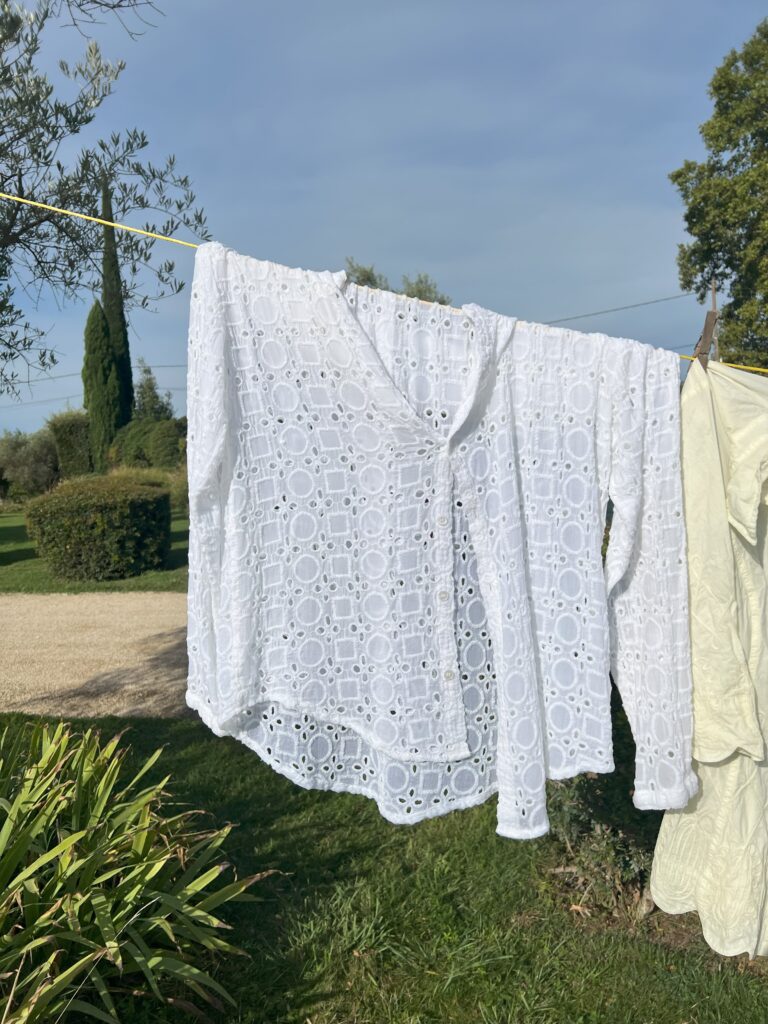
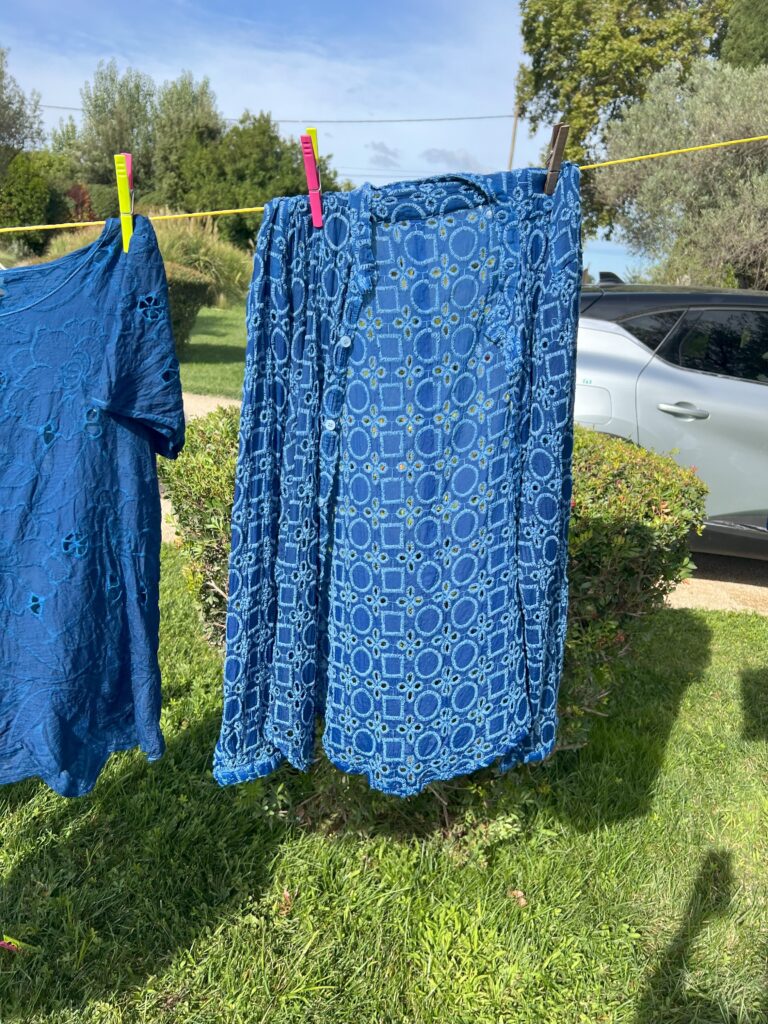
Woad only works on natural fibers, so the nylon threads on this shirt didn’t take the dye. I think the contrast is really fascinating!
Denim is another fabric that works well with woad. I dipped my jeans five times for the deepest color possible, a process called “overdye.”
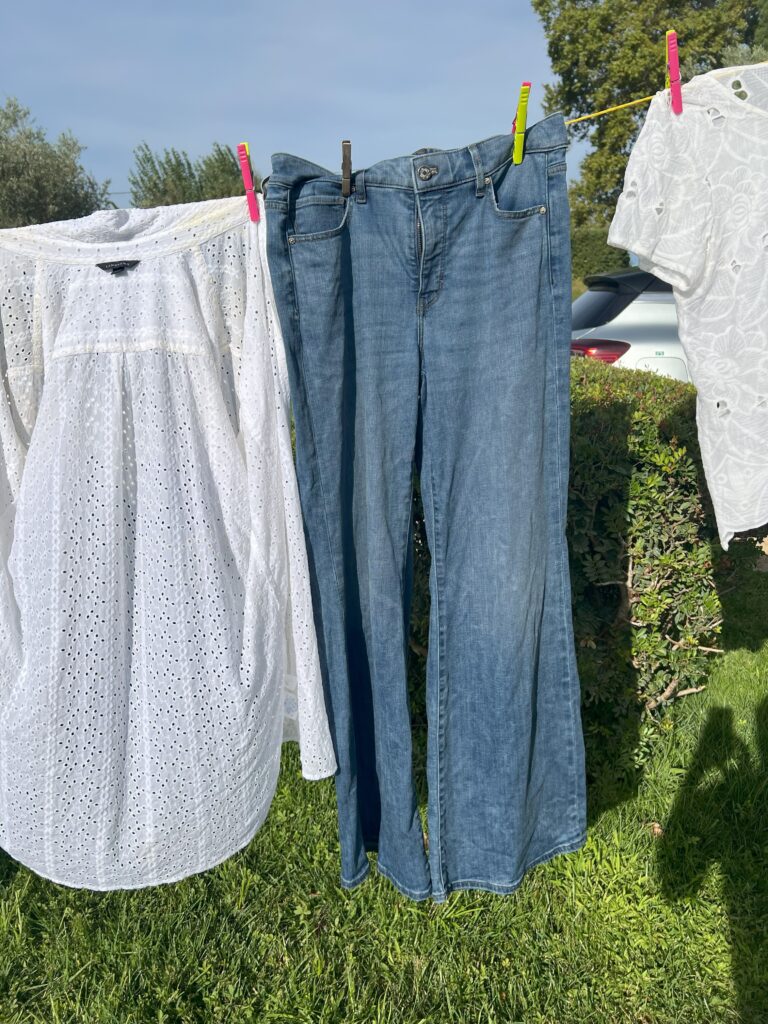
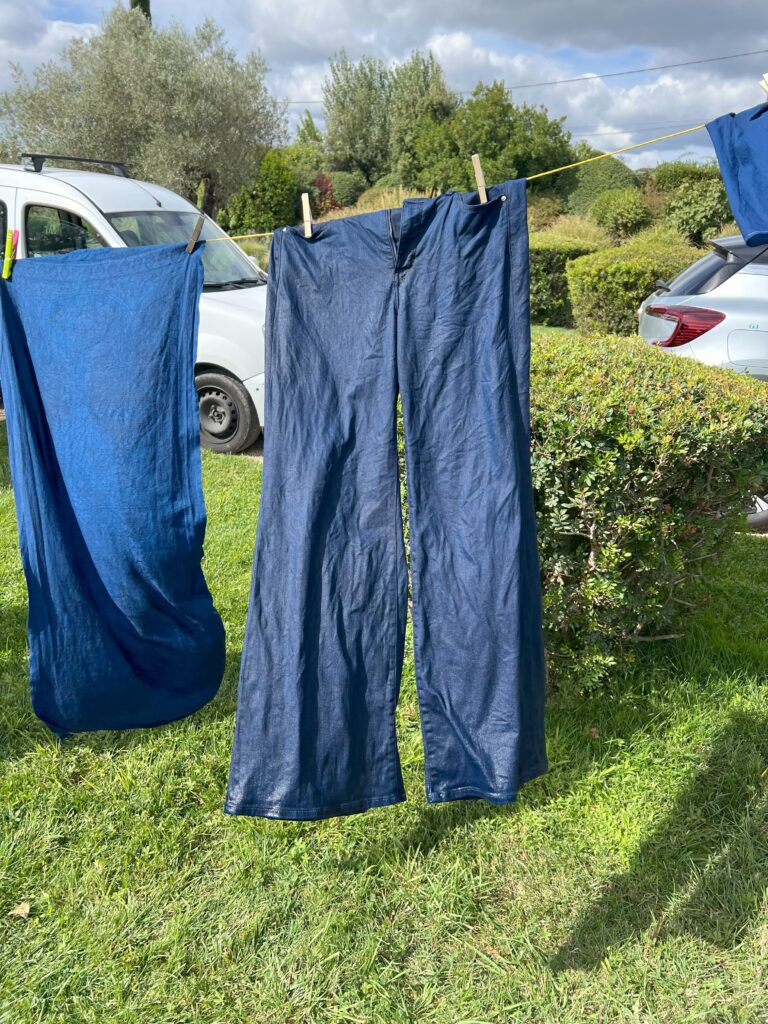
However, there is a point at which the fabric won’t take any more dye. It might not be the color you want, but you have to accept that the content of the fabric dictates the color – not the human dying it!
For example, this wool scarf would only take the color until it was a light sky blue. After that, it refused to get deeper, even with additional dips!
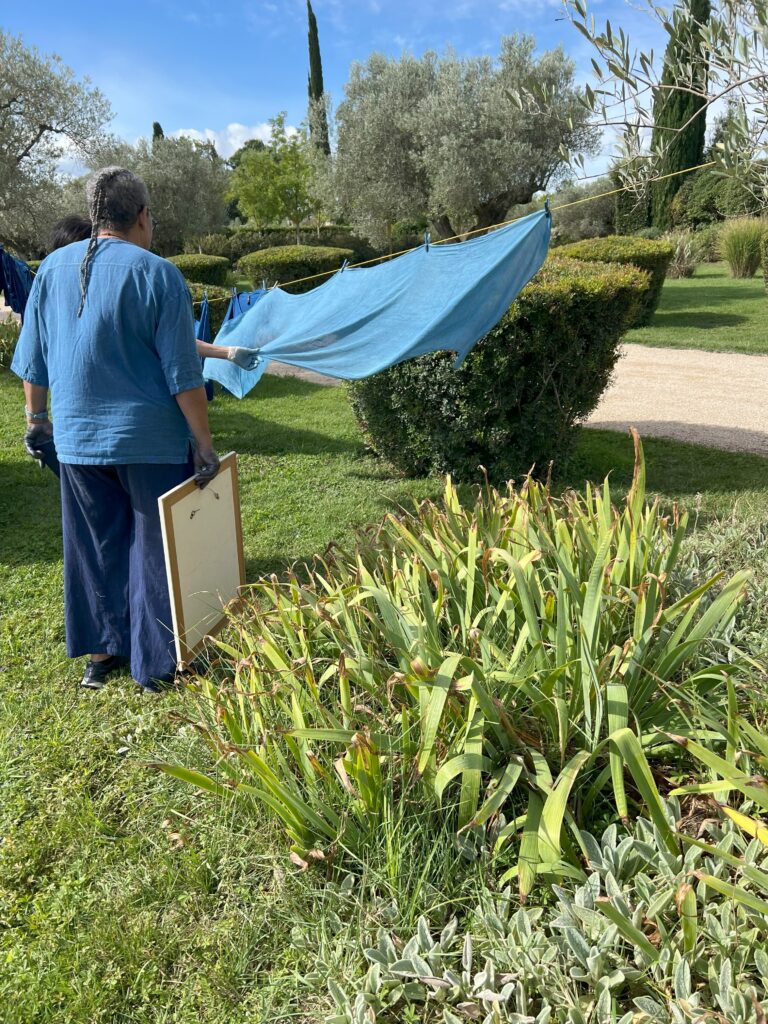
Woad works on lots of colors, not just white and blue. I found this rather ugly gray pillowcase and transformed it into something I plan to actually use in my home! See how the pattern stands out so much more after the dyeing?
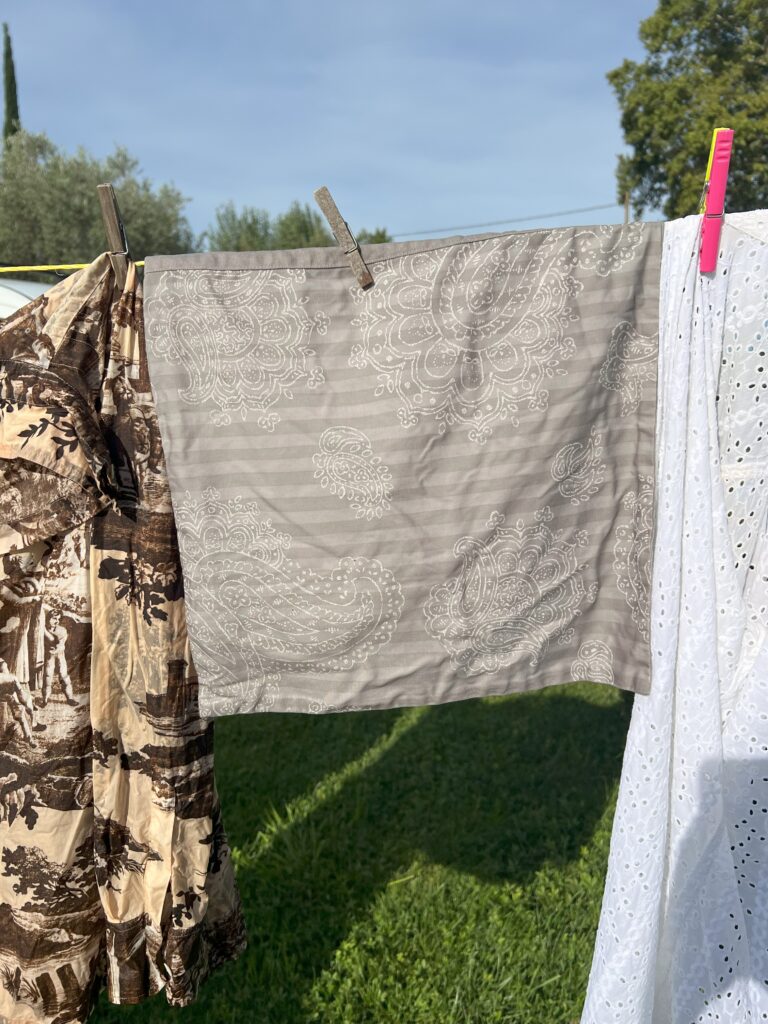
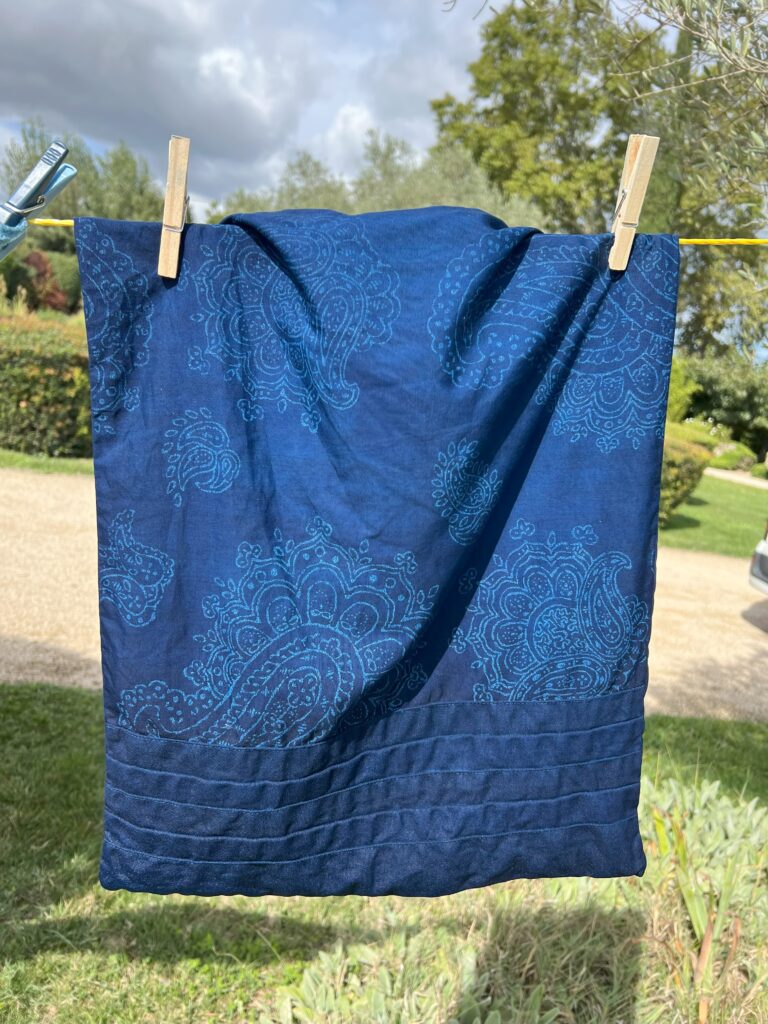
What’s also fascinating is that each batch of woad dye can vary depending on factors such as the plant’s growing conditions, fermentation time, and the number of dips. Sometimes the water itself will affect the dye’s color range.
Learning about woad was a fascinating process! Woad might not be in our everyday wheelhouse, but we’d love to help add color to your home. Book a Discovery Call with us to learn how!
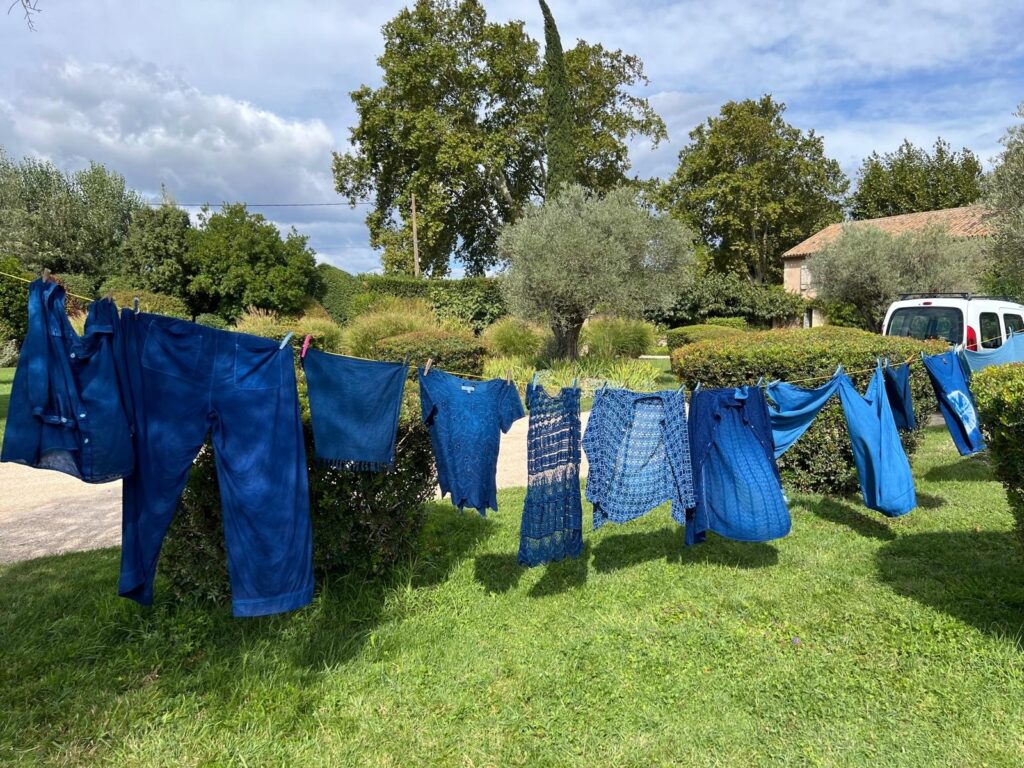